Anything that is going to come into contact with either the lye or the raw soap MUST be made of Stainless steel, glass or a non reactive plastic.
For this project I have amassed;
Various Oils
Castor
Palm
Palm Kernel
Coconut
Essential Oils for scent
Bentonite clay for shaving soaps.
Lye
Distilled water (tap water WILL NOT work, even the super soft water we have here has too high an ion/mineral content and will cause issues)
Personal protective equipment
Gloves
Eye protection
Good ventilation
Access to running water
White Vinegar
Stirring devices, ie. whisk, stick blender.
Digital thermometer (very important)
Hot pads
Glass or stainless steel measuring cups
A semi accurate scale. I use a kitchen scale, +/- 2 grams is not significant in a 5300+gram recipe.
An accurate scale for measuring the lye to .1g (they say .1g but all of these 20$ digital scales seem to be accurate only to ~.2g)
A stock pot (or crock pot for smaller batches)
Reynolds Oven Bags (not actually necessary but these will keep your essential oils and glycerin from boiling off.)
A soap mold (a shoe box lined with parchment or wax paper works as a disposable mold for small batches)
A soap cutter
Packaging if you so desire
Curing space. During the production of soap water is a byproduct of saponification. Letting the cooked soap sit for a couple days in open air will make the soap harder and longer lasting. Time will also allow the soap to mellow. When it's fresh out of the oven there are still some un-reacted products and the soap is slightly basic. (ph ~8) 24-36 hours later (depending on ambient temps and couple of other factors) the soap is done saponifying, and the air is drying the water out of the product.
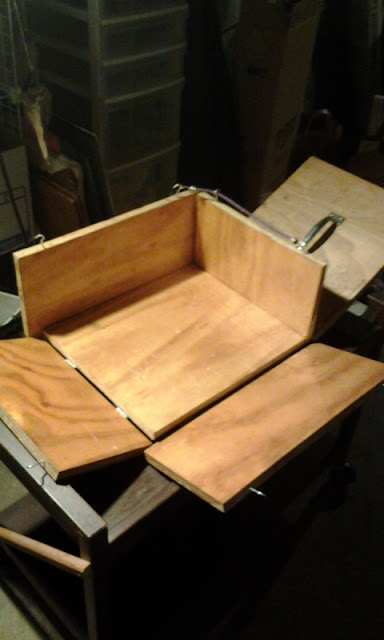 |
My soap form with hinged sides. It will hold up to 50 pounds of soap. The lid is separate and sitting in the back (upper right) |
The form was simple enough the hinges allow the sides to fold away from the soap block. I had trouble with a different mold design, releasing while the soap was warm was destroying batches. Waiting for the soap to fully cool was making the release difficult as well and destroying batches. This was my solution.
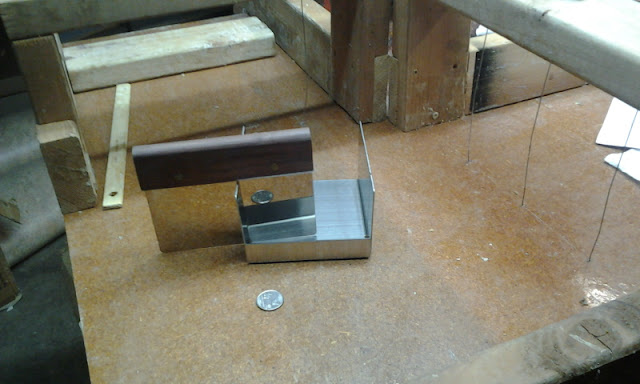 |
A quarter in front of a commercial Stainless cutter sitting on My wire cutter. Which needs a little touch up after 3 moves and 2 years in storage. |
I originally had it set up to cut the entire brick in just a few passes, but the physics of cutting that large a surface were against me. I slice the block into logs, then slice the logs. The stainless cutter in the foreground has never been used, it was presented to me. Had I been making 2 pound batches every week it would have been ideal. At this size of manufacturing its pointless.